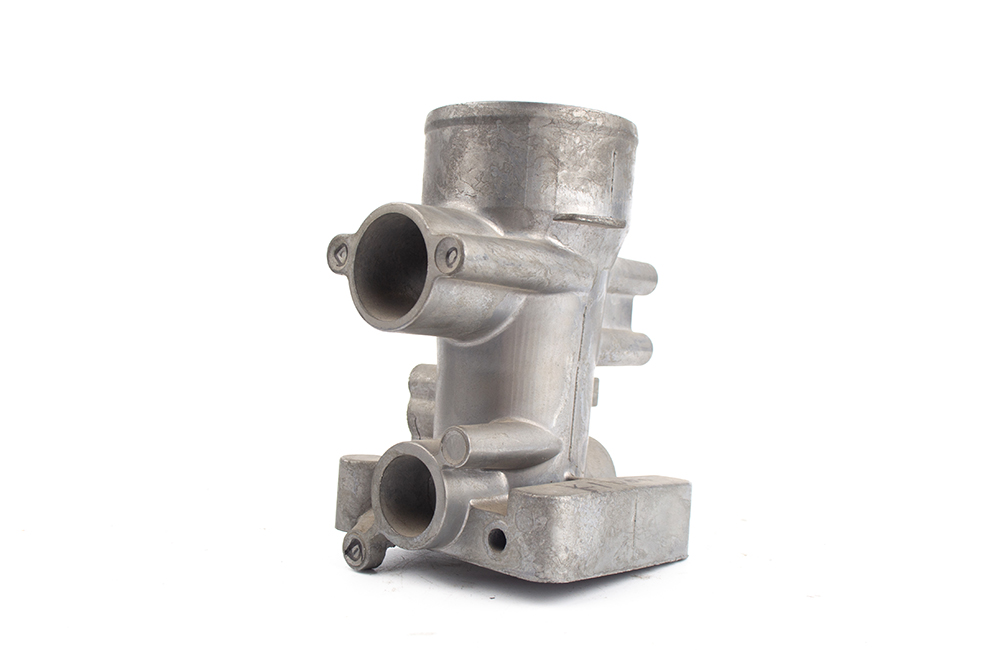
行業(yè)/分類:其他手板模型加工
加工方式: 鈑金 使用材料: 鋁合金
最小精度: 0.1mm 生產(chǎn)周期: 2~7天
產(chǎn)品尺寸: 10cm*5cm*15cm
后處理: 打磨
設計與模具準備
產(chǎn)品設計:使用 CAD 等專業(yè)設計軟件對閥門手板模型進行三維設計,精確規(guī)劃其結(jié)構、尺寸、形狀等,確保符合閥門的實際使用要求和設計理念。
模具設計:根據(jù)產(chǎn)品的三維模型,考慮壓鑄工藝的特點,如金屬流動、收縮率、脫模方式等因素,設計出合理的壓鑄模具結(jié)構。模具通常由定模和動模兩部分組成,需要精確設計各個部件的形狀、尺寸和配合精度5。
模具制造:選用高強度、耐磨性好的合金鋼材料,通過機械加工、電火花加工等工藝制造壓鑄模具,確保模具的精度和表面質(zhì)量,以保證壓鑄出的閥門手板模型具有良好的尺寸精度和表面光潔度。
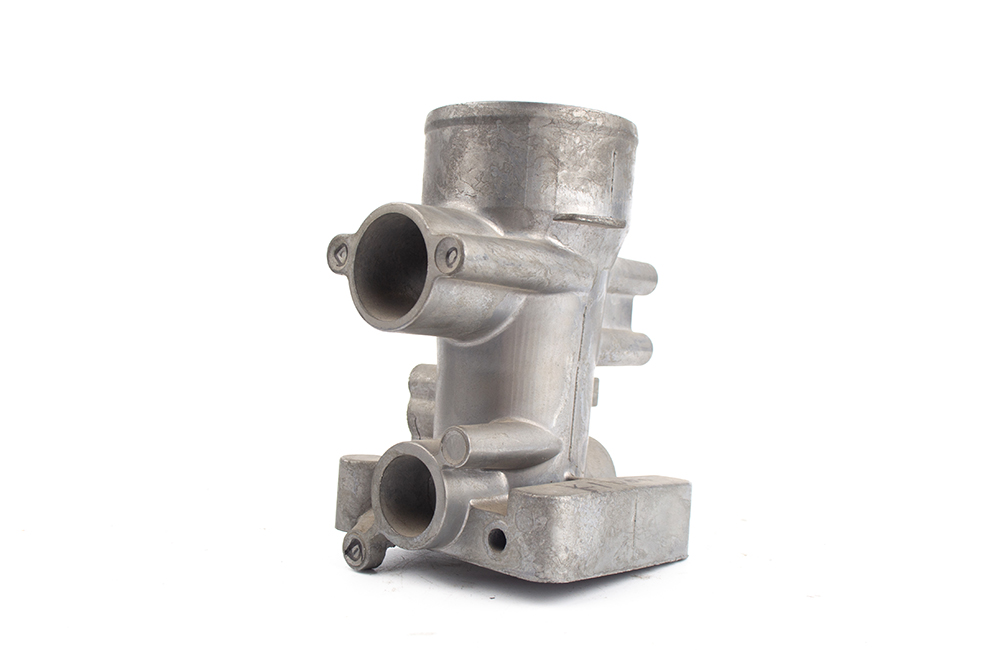
材料選擇與熔煉
合金選擇:根據(jù)閥門手板模型的使用要求和性能特點,選擇合適的壓鑄合金,如鋁合金、鋅合金或鎂合金等。鋁合金具有密度小、強度高、耐腐蝕性好等優(yōu)點;鋅合金流動性好、成本較低;鎂合金則具有更高的比強度和比剛度。
材料檢驗:對所選的合金材料進行質(zhì)量檢驗,確保其化學成分和物理性能符合要求,避免因材料質(zhì)量問題導致的產(chǎn)品缺陷。
熔煉:將經(jīng)過檢驗合格的合金材料放入熔煉爐中,加熱至適宜的溫度使其熔化,同時進行攪拌和精煉等操作,去除雜質(zhì)和氣體,提高合金液的質(zhì)量。
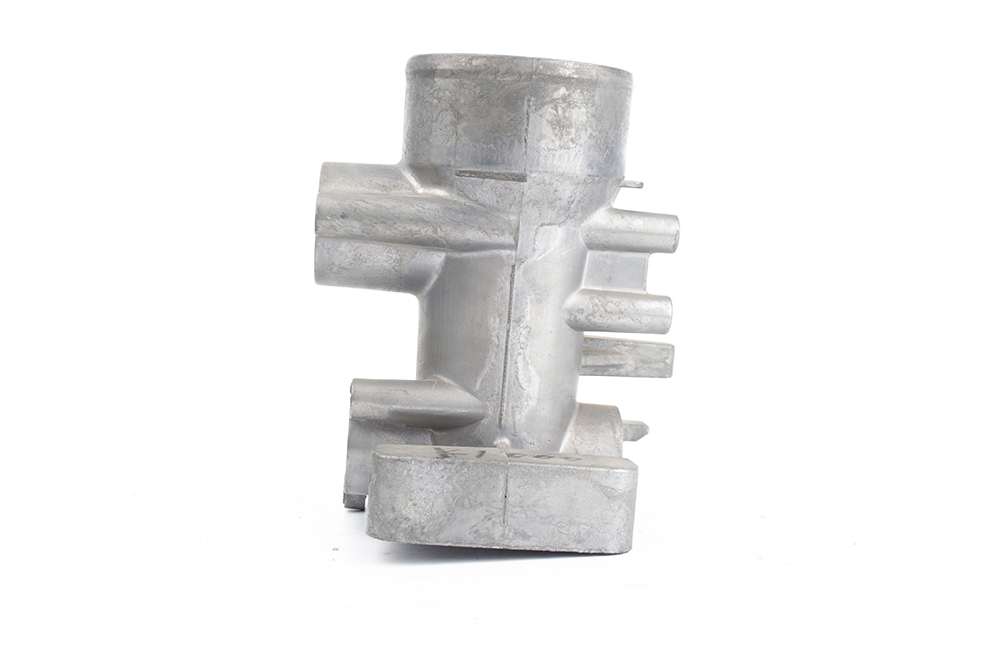
壓鑄過程
模具預熱:在壓鑄前,將壓鑄模具預熱至一定溫度,通常在 150℃-300℃之間,以減少模具與高溫合金液的溫差,避免模具因急冷急熱而產(chǎn)生熱裂紋,同時提高合金液在模具內(nèi)的流動性。
高壓注射:將熔化好的合金液在高壓下注入模具型腔,注射壓力通常在幾十兆帕到幾百兆帕之間,使合金液能夠快速填充模具型腔,形成閥門手板模型的雛形。
保壓與冷卻:在合金液填充型腔后,保持一定的壓力一段時間,使合金液在壓力下進行凝固收縮,以補充因凝固而產(chǎn)生的體積收縮,提高產(chǎn)品的致密度和尺寸精度。然后,通過模具內(nèi)的冷卻通道,對模具進行冷卻,使合金液快速凝固成型。
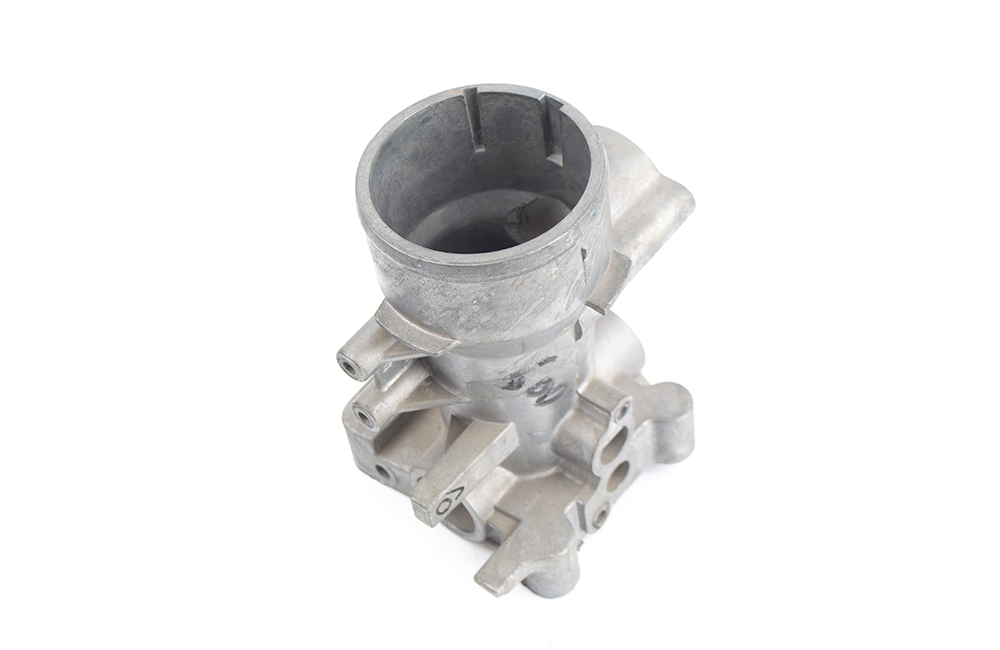
后處理
脫模與去毛刺:當模具內(nèi)的合金液凝固成型后,打開模具,取出閥門手板模型,并去除模型上的毛刺、飛邊和澆口等多余部分,可以使用手工打磨、機械去毛刺等方法。
表面處理:根據(jù)閥門手板模型的外觀和使用要求,對其進行表面處理,如噴砂、拋光、電鍍、氧化等。噴砂可以提高表面粗糙度,增強涂層的附著力;拋光可以使表面更加光滑,提高外觀質(zhì)量;電鍍和氧化可以提高耐腐蝕性和耐磨性。
整形與校正:對于在壓鑄過程中可能出現(xiàn)的變形或尺寸偏差,采用整形和校正工藝進行修復,如使用夾具進行固定、機械校正等方法,確保產(chǎn)品的尺寸精度和形狀符合設計要求。
質(zhì)量檢驗
尺寸檢查:使用量具,如卡尺、千分尺、三坐標測量儀等,對閥門手板模型的各個尺寸進行測量,確保其尺寸偏差在設計要求的公差范圍內(nèi)。
外觀檢查:目視檢查產(chǎn)品的外觀質(zhì)量,包括表面光潔度、有無氣孔、砂眼、裂紋等缺陷,對于表面質(zhì)量要求較高的產(chǎn)品,還可以采用光學顯微鏡、電子顯微鏡等儀器進行檢查。
性能測試:根據(jù)閥門手板模型的實際使用要求,進行相應的性能測試,如密封性測試、耐壓測試、開閉扭矩測試等,以驗證產(chǎn)品是否滿足設計要求和使用性能。