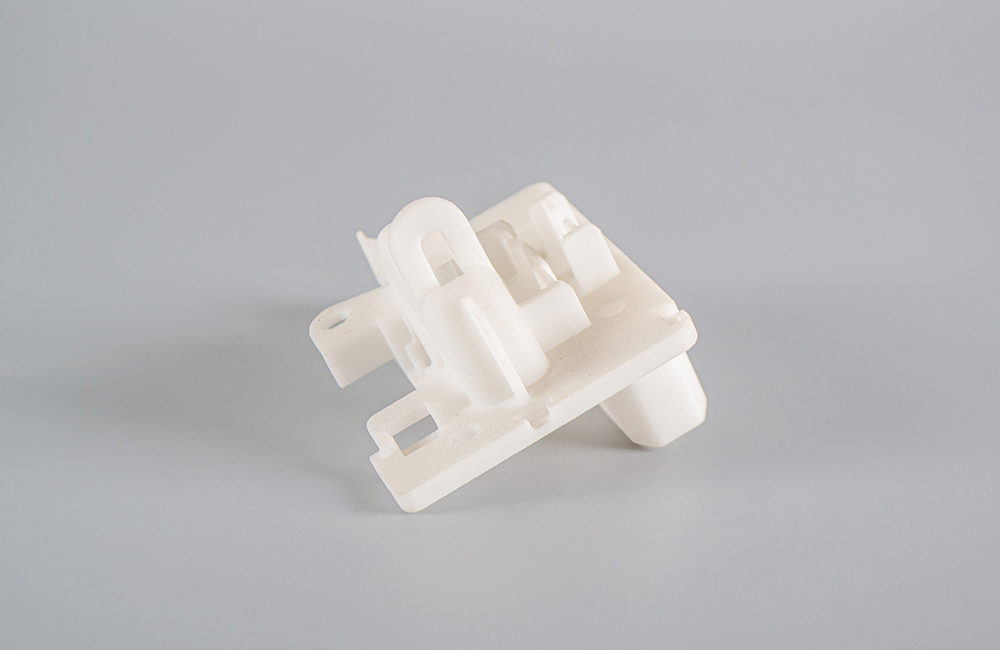
行業(yè)/分類:其他手板模型加工
加工方式: 3D打印 使用材料: 樹脂
最小精度: 0.1mm 生產(chǎn)周期: 2~7天
產(chǎn)品尺寸: 5cm*5cm*4cm
后處理: 打磨
優(yōu)點
縮短研發(fā)周期:傳統(tǒng)制造手板模型的方式往往需要經(jīng)過多道復雜工序,耗時較長。而 3D 打印技術能夠直接根據(jù)設計模型快速制造出零件手板模型,大大減少了從設計到實物的時間,使通訊器材的研發(fā)進程加快,更快地推向市場。
降低成本:在產(chǎn)品開發(fā)初期,若采用傳統(tǒng)制造方式制作模具來生產(chǎn)少量的手板模型,成本會很高。3D 打印無需制作復雜的模具,只需有數(shù)字模型文件即可進行打印,尤其對于小批量、復雜結構的通訊器材零件手板模型制作,成本優(yōu)勢明顯。
高度定制化:通訊器材的更新?lián)Q代快,對個性化和定制化的要求也越來越高。3D 打印技術可以根據(jù)不同的設計需求,輕松實現(xiàn)各種復雜形狀和結構的零件手板模型制造,滿足通訊器材多樣化的設計要求,為產(chǎn)品創(chuàng)新提供了更大的空間。
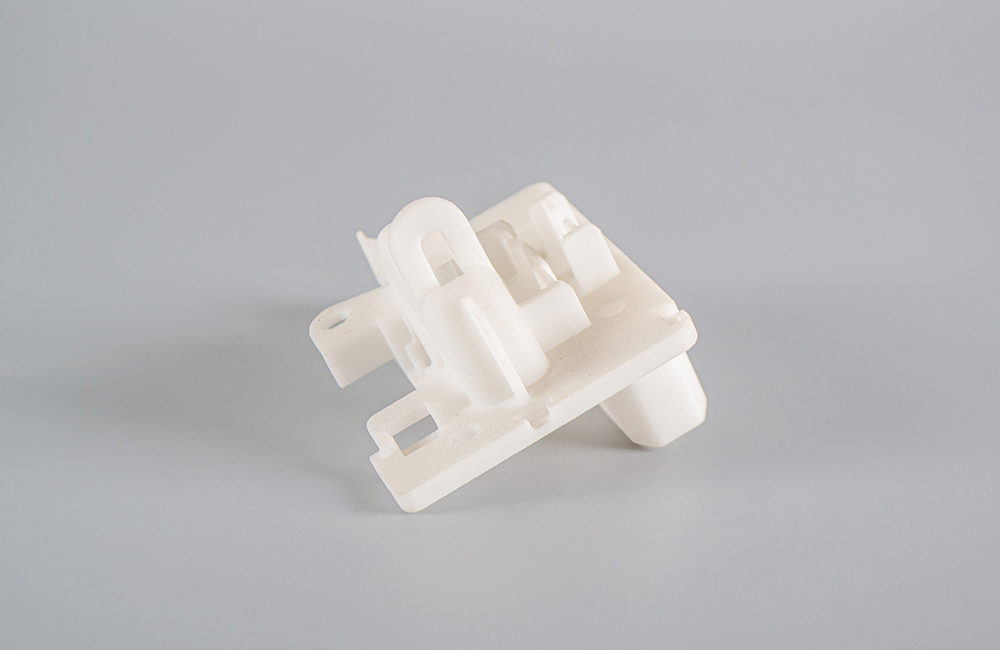
精度較高:目前的 3D 打印技術已經(jīng)能夠達到較高的精度,可以滿足通訊器材零件手板模型對于尺寸精度和細節(jié)表現(xiàn)的要求,從而更準確地驗證產(chǎn)品的設計和功能。
常用材料
光敏樹脂:具有精度高、表面質(zhì)量好的特點,能夠打印出非常精細的結構和光滑的表面,適合制作對外觀和細節(jié)要求較高的通訊器材零件手板模型,如手機外殼、按鍵等。
ABS 塑料:具有良好的機械性能和穩(wěn)定性,強度較高,韌性較好,適用于制作一些需要承受一定外力或具有一定結構強度的通訊器材零件手板模型,如通訊設備的支架、外殼等。
尼龍:具有較高的強度和耐磨性,同時還具備一定的柔韌性,適合制作一些需要具備耐磨、耐腐蝕等特性的通訊器材零件手板模型,如連接器、插頭等。
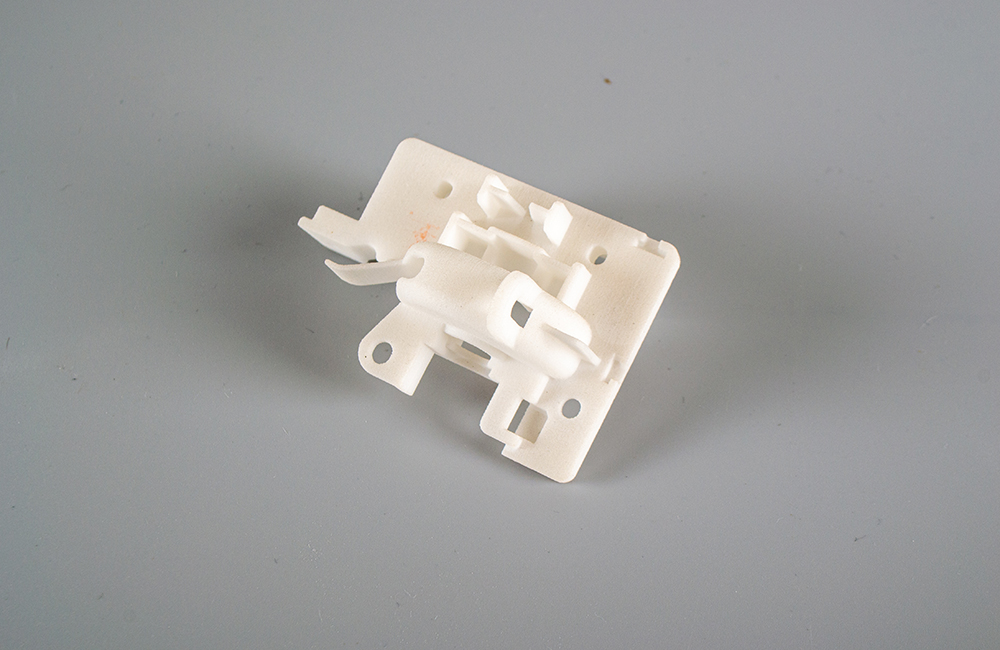
制作流程
3D 建模:設計師根據(jù)通訊器材零件的設計要求,使用專業(yè)的 3D 建模軟件創(chuàng)建零件的三維模型。在建模過程中,需要考慮零件的尺寸、形狀、結構、裝配關系等因素,以確保模型的準確性和可制造性。
模型修復與優(yōu)化:對創(chuàng)建好的 3D 模型進行檢查和修復,確保模型沒有錯誤和瑕疵。同時,根據(jù) 3D 打印的工藝特點和要求,對模型進行優(yōu)化,如調(diào)整模型的壁厚、添加支撐結構等,以提高打印的成功率和質(zhì)量。
選擇 3D 打印設備和材料:根據(jù)通訊器材零件手板模型的具體要求,選擇合適的 3D 打印設備和材料。不同的 3D 打印設備和材料具有不同的性能和特點,需要綜合考慮零件的尺寸、精度、強度、外觀等因素來進行選擇。
3D 打印:將優(yōu)化后的 3D 模型導入到選定的 3D 打印設備中,進行打印參數(shù)的設置,如打印層厚、打印速度、曝光時間等。設置好參數(shù)后,啟動 3D 打印機進行打印,打印過程中需要注意觀察打印情況,確保打印的順利進行。
后處理:打印完成后,需要對零件手板模型進行后處理,包括去除支撐結構、打磨、拋光、噴漆、電鍍等工藝,以提高模型的表面質(zhì)量和外觀效果,使其更接近最終產(chǎn)品的要求。
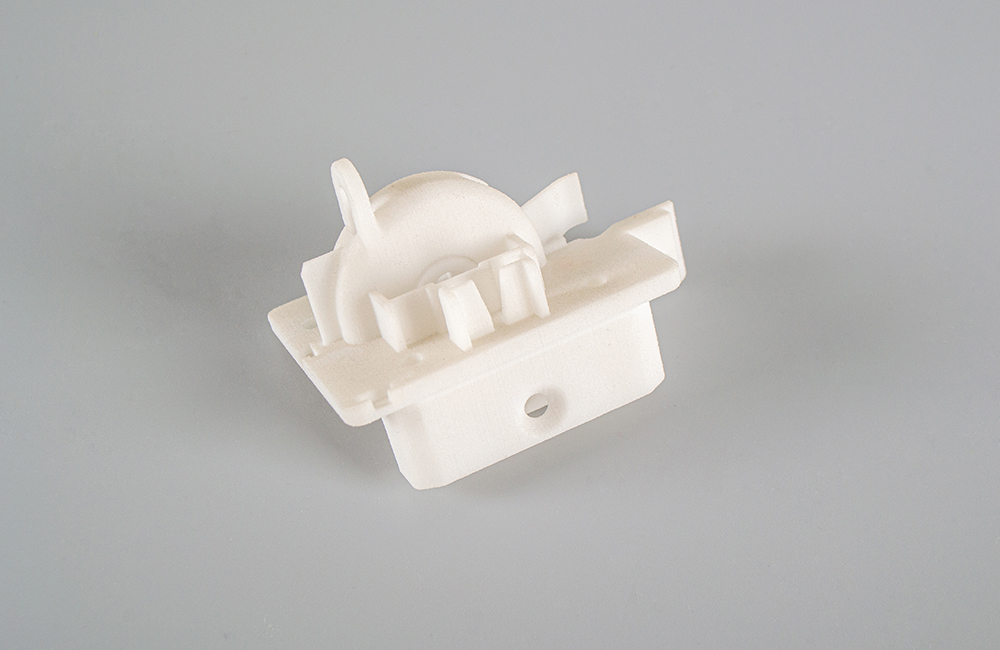
質(zhì)量檢測:對經(jīng)過后處理的通訊器材零件手板模型進行質(zhì)量檢測,主要包括尺寸精度檢測、外觀檢查、裝配測試等。確保手板模型符合設計要求和質(zhì)量標準,能夠滿足通訊器材的研發(fā)和測試需求。
應用案例
手機配件:如手機外殼、按鍵、攝像頭模組、耳機插孔等零件的手板模型制作。通過 3D 打印技術,可以快速制造出不同設計方案的手機配件手板模型,進行外觀和功能的驗證,為手機產(chǎn)品的研發(fā)和改進提供依據(jù)。
基站設備:基站設備中的一些復雜結構零件,如濾波器、天線支架、散熱器等,也可以采用 3D 打印技術制作手板模型。這些零件通常具有復雜的形狀和結構,傳統(tǒng)制造方式難度較大,而 3D 打印可以輕松實現(xiàn)其制造,幫助工程師更好地進行設計優(yōu)化和性能測試 。
光通訊器件:光通訊器件對精度和表面質(zhì)量要求較高,3D 打印技術可以制造出高精度的光通訊器件手板模型,如光纖連接器、光分路器等,用于光學性能測試和結構驗證,提高光通訊產(chǎn)品的研發(fā)效率和質(zhì)量 。